Darkly Labs has achieved great success since the launch last year of the Emblaser, an entry-level laser cutter and engraver kit developed by the Melbourne-based company to fill the gap in the market of affordable desktop laser cutters.
Domenic Di Giorgio, the founder of Darkly Labs, took an innovative approach to funding, designing and manufacturing the Emblaser, challenging the traditional methods of developing a product. This involved the use of crowd-sourcing and 3D printing to get to market faster and at a lower cost. The company utilised 3D printing to build most of the components for the Emblaser, as it was more cost effective for producing a low volume of laser cutters. It was also a great solution when it came to making prototypes as well as actual parts, because modifications to designs could be easily managed by the Darkly Labs’ team.
Darkly Labs launched the Emblaser in 2014, selling over 800 units to hobbyists in the US, Asia, Australia and Europe. The product can be used to cut or engrave flat sheet materials such as paper, wood, plastic and fabric. Universities also use it for research and student projects in many departments.
Creating and launching a new product:
Darkly Labs faced many challenges in developing the Emblaser, with the first hurdle to overcome being funding. The company financed the project by raising more than $500,000 on the crowd-funding website Kickstarter. This was the third-largest amount of funding raised for an Australian Kickstarter project in 2014. The enthusiastic response also proved that there was a viable untapped market segment
The second dilemma was to create a high-tech piece of technology for the mass market with a very small team and limited time. This was overcome by working with experts in the field and advanced manufacturing techniques.
Darkly Labs decided to use 3D printing for the design and manufacture and looked for suppliers who wanted the team to succeed. As a result the company didn’t follow the industry-accepted method of production, preferring an innovative and flexible approach. The team was able to use 3D printing to design and manufacture components for the laser cutter. It was also reliable, ideal for testing components and made assembly of components an easy process.
Finally, Darkly Labs needed to find efficient ways to support and educate its customers as they were introduced to a new piece of technology.
“We spent a great deal of time developing documentation as customers assembled the kits and needed to have clear instructions,” says Di Giorgio. “The aim was to keep it simple and informative”.
Low-volume manufacturing:
Darkly Labs purchased a Stratasys Dimension Elite 3D printer from local supplier Tasman 3DPrinters.
“We had previous good experience with Stratasys’ 3D printers and the local distributor Tasman 3DPrinters was able to provide fantastic and expert technical support,” says Di Giorgio. “The reliability and accuracy of the Dimension Elite 3D Printer was a key requirement for us.
“Tasman 3DPrinters had a great understanding of our need and had excellent customer service for any technical enquiries and ordering of material supplies. They supported us as we developed our product and launched it in the market.”
According to Di Giorgio, the Stratasys machine, along with support from Tasman 3DPrinters, have been crucial in allowing Darkly Labs achieve its goals.
“Setting up the Stratasys 3D printers in our business resulted in real benefits. The time required to design, create prototypes and test timeframes was significantly lower compared to traditional methods. The development costs were lower and small production runs were possible”.
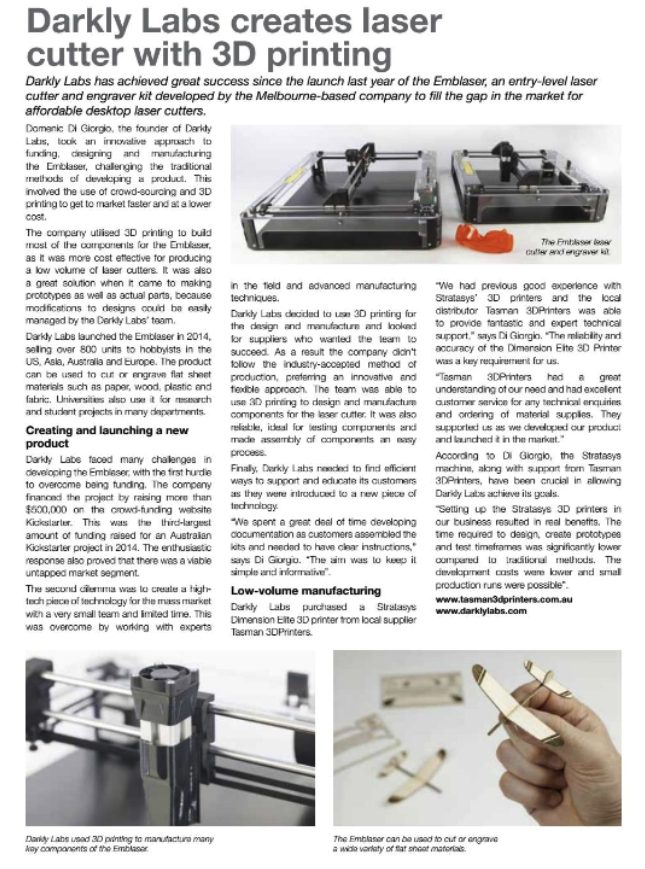